Woodworking in America 2013 is just around the corner. If youre planning on attending, Im sure youre getting excited about a weekend of non-stop woodworking discussion already. If youve attended previous WIAs you know that the talk of - and camaraderie around - woodworking extend well past the actual conference hours of about 8:30 am to 6:00 pm.
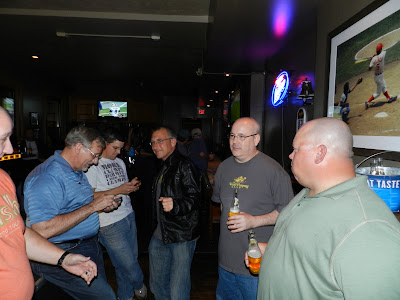 |
Steve, Niks Dad, Sean, Vic, Kyle & Matt have fun at Keystone |
Each night of the conference (Thursday, Friday & Saturday) there are official (& Semi-Official) Activities. There is the Lost Art Press Thursday night Roubo release party, the official Friday Night WIA Banquet and the Saturday Evening Planemakers Dinner. These are wonderful activities where you can relax and enjoy with our woodworking friends.
Dont be fooled though. There is so much more going on at WIA at night.
If youve heard me talk about WIA or FWWLive or any other woodworking conference on the Modern Woodworkers Association Podcast, youve heard me say over and over how the best part of the conferences is the community of fellow woodworkers who you meet and socialize with over the event. Evening is a prime time for this to happen. |
We work wood and eat German food (and were loud). |
The Modern Woodworkers Association has setup and is helping promote meetups every night of the conference. All are free to enter (you pay for your own food & drink) and all will be attended by fellow woodworkers. Thursday: MWA Meetup at KeystoneBeginning at 7:00 pm, well be hanging out in the upstairs bar room at the Keystone Bar & Grill. Its a quick walk from the convention center and most of the hotels. Meeting at the Keystone on the opening night of registration has become a tradition for WIA and we hope youll join us. Many fellow MWA members, woodworking bloggers and other WIA attendees will be there. If youre going to to the Roubo Book Release, dont worry. You can join us at Keystone afterwards. All are welcome.
Friday: HofbrauhausThe Hofbrauhaus excursion on Friday night is another WIA tradition. Its less organized than the meetups at Keystone, in that we dont reserve a private room. We just jump on the trolley and head to Hofbrauhaus. Its a fun night of great beer, great food, great company and loud music. If youre going to the official WIA Banquet, please join us at Hofbrauhaus afterwards. We usually stay late. If youre looking to meet us at Hofbrauhaus, theres no telling exactly where well be, though in past years weve started the evening at the outside bar area and then moved to one of the many long tables. Just listen for Tom Iovino and youll be sure to find us. All are welcome.
Saturday: WoodTalk Meetup at Keystone
The WoodTalk guys have setup their own Meetup at the Keystone on Saturday night. It begins at 6:30. Since it was organized by and features Marc, Matt & Shannon, you should expect that this will be the smoothest running event of the weekend. Still, its going to be an absolute blast and all should come. I know were going to try to represent the MWA there in force.
Afterwards:Just about every night some folks will stop by the Behle St Cafe before heading back to their rooms. If its late, but youre still looking to hang out with woodworkers, joint us there. All are welcome.
Venue Information
Keystone Bar & Grill
313 Greenup St
Covington, KY
Hofbrauhaus Newport
200 East 3rd St
Newport, KY 41071
Take the SouthBank Shuttle (trolley) to the stop between Monmouth St & Saratoga St (it doesnt have stop names)
Behle St Cafe
50 East Rivercenter Blvd
Covington, KY 41011
Across the street from the convention center in the same building as the Embassy Suites
?
?
Dont forget about the +Modern Woodworkers Association Podcast. We talk woodworking with Guests from around the world of woodworking every other week. Subscribe to the RSS feed or iTunes today.